Impact Windows on Commercial Buildings In Florida: Rules & Regulations
Ever stared at a skyscraper and marveled at the glass windows gleaming against the skyline? Each of those windows, believe it or not, is subject to rigorous regulations and certifications. The story behind each pane is one of resilience in the face of extreme weather conditions, energy efficiency demands, local code compliance, and so much more.
Are there specific regulations or certifications that impact windows in commercial buildings must meet? Yes indeed! And understanding these can be like navigating a labyrinth for property owners or contractors alike. This blog post will serve as your trusty guide through this maze.
You’ll gain insights into how building codes shape window specifications – from Florida’s unique requirements to international standards set by councils worldwide. You’ll learn about key certifications for safety and energy conservation, and get an insider look into what goes on during installation processes, including testing protocols for compliance.
Table of Contents
Building Codes and Regulations for Impact Windows
If you’re considering replacement windows in Florida, understanding the local building codes is crucial. They set specific performance requirements for commercial buildings to withstand high wind speeds and windborne debris.
The primary governing body here is the International Code Council (ICC). Their standards, like the design pressure rating and wind loads, are widely used around the globe. For an overview of ICC’s adoption chart, please refer to the provided link.
Understanding Miami-Dade County’s Unique Requirements
Miami-Dade County requires its own special considerations when it comes to building construction. It not only considers typical factors such as wind pressures but also includes details from intricate wind speed maps. This approach helps ensure each building gets an appropriate level of hurricane protection.
A significant aspect of these guidelines is established by the International Residential Code (IRC) and the International Energy Conservation Code (IECC), which provide further insights into how your replacement window should perform under extreme weather conditions.
Certifications and Standards for Impact Windows
Impact windows need to meet specific standards to be deemed safe and energy efficient. One such standard is the ASTM E1886-13a, which tests how these products fare under extreme environmental conditions.
The other certification, ASTM E1996-2014a, checks a window’s ability to withstand windborne debris during storms. It’s critical because Florida homes often face hurricane-level windspeeds.
Unpacking the International Energy Conservation Code
This code focuses on energy efficiency in commercial buildings. Products must also pass testing set by associations like FGIA (Fenestration and Glazing Industry Alliance). These groups ensure that manufacturers uphold industry-wide standards of quality.
With this information, you can make sure your replacement windows not only look good but are durable too. They’ll help protect your home from harsh weather while conserving energy – talk about a win-win situation.
Installation and Performance Path for Impact Windows
The process of installing impact windows involves careful attention to the building envelope. The goal is to minimize air infiltration through exterior openings, especially around windows.
To meet standards, these products must pass specific requirements. For instance, they need to demonstrate low air infiltration and water penetration, while providing structural performance that can withstand Florida’s harsh weather conditions.
AAMA 506, a comprehensive guide on installation practices, is an invaluable resource in this regard.
The Role of Fasteners in Securing Impact Windows
In securing impact windows against extreme wind speeds, fasteners play a critical role. These secure exterior windows firmly into place within the building envelope.
These tiny components are responsible for ensuring your window remains intact during hurricane-level winds or other extreme weather events common in Florida. Properly installed fasteners help ensure your window performs as expected when it matters most.
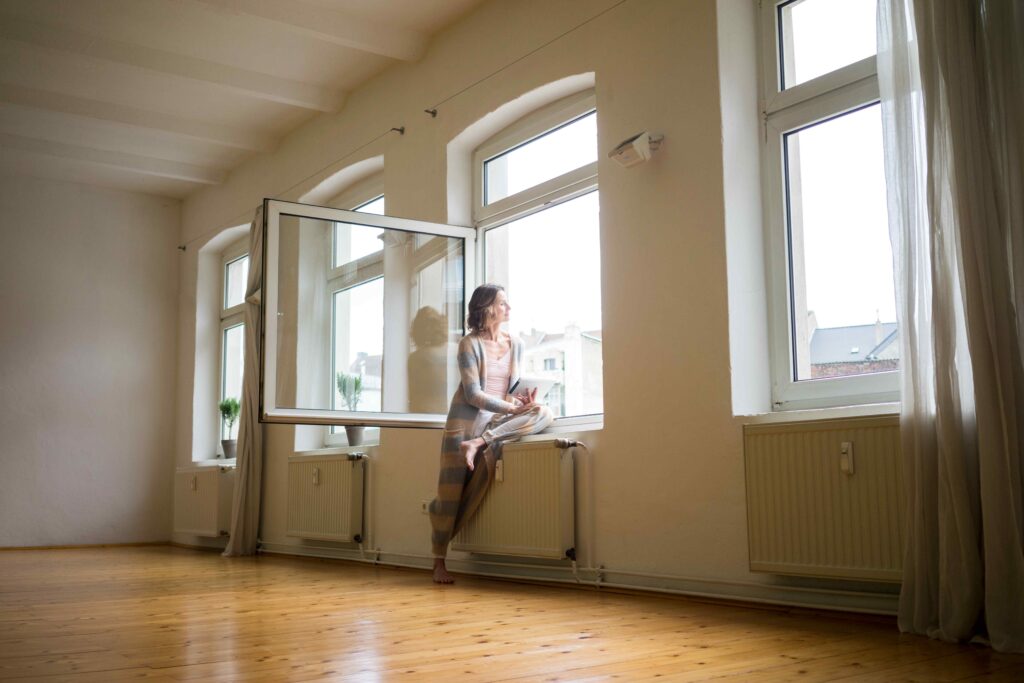
Compliance and Testing of Impact Windows
If you’re wondering how impact windows prove their mettle, it all starts with rigorous testing. These products must face trials by standards such as ASTM E1886-13a and ASTM E1996-2014a, akin to a window gladiator fighting in the arena against wind speeds.
How Products Meet Wind Pressure Requirements
The crux lies in ensuring that these replacement windows can withstand the wrath of Mother Nature. They are like soldiers on the frontline, holding back storm winds and hurricane-level pressure.
To confirm compliance, manufacturers put them through simulations replicating extreme weather conditions – imagine recreating scenes from “Twister” but for window testing.
A pass mark not only shows they meet specific requirements but also serves as an assurance that your Florida building will be well protected during harsh weather. The hero behind this safety? The AAMA 506 certification label tab; think of it as a badge of honor for each tested product.
In essence, complying with regulations is more than just crossing t’s or dotting i’s – it’s about delivering top-notch performance under pressure, quite literally.
Energy Efficiency Requirements for Impact Windows
The heart of energy efficiency in commercial buildings lies within the SHGC requirements and the use of laminated glass. This dynamic duo plays a vital role in conserving energy.
The Solar Heat Gain Coefficient (SHGC) is one important requirement to consider when installing impact windows. Lower SHGC values indicate that less solar heat gets through, making your building more efficient by reducing cooling costs.
Laminated glass takes this a step further with its additional layer of polyvinyl butyral (PVB). It not only adds an extra level of protection against wind-borne debris during Florida’s hurricane season, but it also contributes significantly to insulation and sound reduction.
These requirements are clearly outlined in the 2018 International Energy Conservation Code (IECC). The IECC sets performance standards for residential buildings’ energy usage including different paths to compliance available for window manufacturers.
A key element addressed by these codes is air leakage resistance which must be determined according to specific guidelines before installation can begin. Adhering strictly to these regulations will help make sure your beautiful Florida commercial building stays cool, comfortable, and resilient all year round.
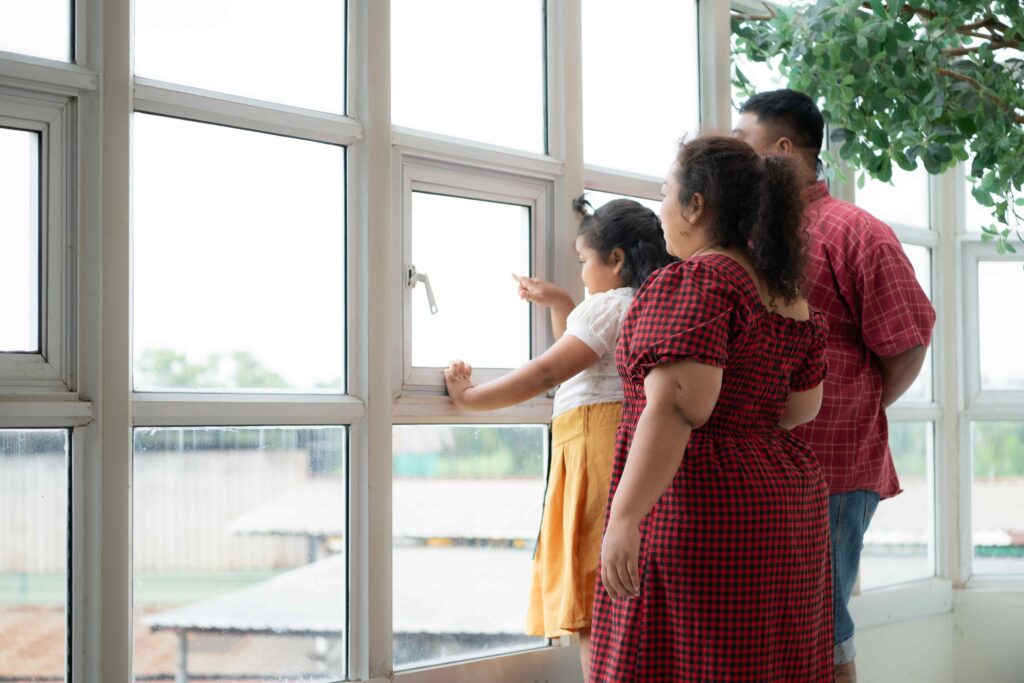
FAQs: Impact Windows on Commercial Buildings In Florida: Rules & Regulations
What are the building regulations for windows?
Building codes, like the International Residential Code and Florida Building Code, dictate window standards. These codes cover design pressure rating, wind loads, and more.
What is the ‘25 rule’ for windows in Florida Building Code?
The ’25 rule’ states that if over 25% of a home’s openings are replaced within one year, all must be upgraded to meet hurricane protection standards.
How do I know if my windows are impact resistant?
Your windows should have an AAMA certification label tab or another trusted mark showing they’ve passed ASTM E1886-13a and ASTM E1996-2014a testing requirements.
What is a code for a window?
‘Code’ refers to legal requirements set by local jurisdictions on factors such as size and placement. This ensures safety measures like emergency escape routes in sleeping rooms/basements.
Conclusion
Impact windows, as we’ve learned, aren’t just glass and frames. They’re a product of careful planning and stringent regulations. The answer to “Are there specific regulations or certifications that impact windows in commercial buildings must meet?” is yes!
You now understand the critical role of building codes, from Florida’s unique stipulations to international standards set by councils like the ICC.
You’ve also explored how key certifications ensure safety and energy conservation while revealing how products undergo rigorous testing for compliance.
And let’s not forget about installation processes – where every fastener counts – contributing towards creating secure building envelopes.
In short: next time you look at those gleaming panes on a skyscraper, remember – there’s more than meets the eye!