Florida Building Codes For Windows
Traditionally, a window’s primary purpose has been to let natural light and fresh air into a building. A window in a Florida building, however, has a rather complex task due to existing code requirements for wind design and energy efficiency. It needs to let some sunlight in while keeping the humidity down. Florida windows need to be able to seal in the conditioned cold temperature without letting moisture develop on the inside of the window. In the summer, it must keep out the sweltering and humid air outside; and in the winter, it must keep the heated air inside.
A Florida window has to hold up to the strong winds of a storm and the wind-driven rain that can soak through weaker structures. The possibility of interaction with flying debris also necessitates resistance or protection in certain locations. Where the planned wind speed is at least 130 mph and within a mile of the coast, and where the actual wind speed is expected to be 140 mph or greater, the Florida Building Code (FBC) mandates impact-resistant or shielded windows.
An obvious example of a complicated system, a window must meet standards for energy economy as well as resistance to wind and water intrusion. The system consists of the window (glass), the frame, the casement, the framing, and the movable components. Window Replacement Company, as a certified contractor of windows and glass doors, is familiar with all building regulations pertaining to your windows. The Florida Building Codes for Windows are complex, but this resource will help you navigate the labyrinth.
Design Wind Pressure Rating
A design wind pressure (DP) rating is one of the more basic performance criteria a window must meet. A window’s DP rating is the design wind pressure it must withstand in accordance with the regulation.
Design wind pressure is determined by a number of variables, including site design wind speed, topography (Exposure Category), structure height, window dimensions, and window position.
Consider a structure with an average roof height of 20 feet situated within 100 feet of the shore, where the design wind speed is 150 miles per hour. What is the minimum wind speed that must be considered during the planning phase for a window with a 10 square foot effective wind area that is situated close to a building corner (Zone 5)?
For a building with a 30-foot average roof height and an Exposure Category B wind zone, the minimum and maximum allowable design wind pressures are +24.3 and -32.5 pounds per square foot, respectively (psf). The building’s proximity to the water suggests that it falls into Exposure Group D. As a result, the necessary design wind pressure can be modified by selecting the proper factor from the Florida Building Code, Residential (FBCR) reference table. Therefore, the window’s DP rating must be greater than or equivalent to +37.7 and -50.4 psf.
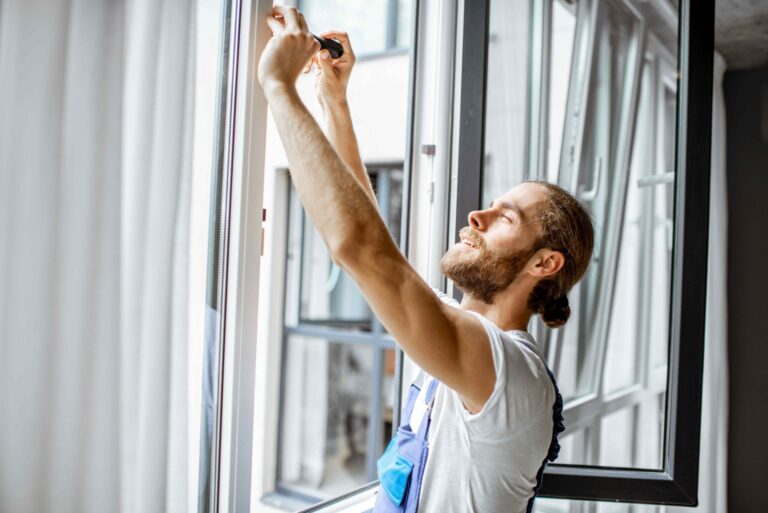
How Windows Are Tested
Installations of glass doors and windows in external wall systems are subject to the FBC’s building and performance standards. Labels that are approved need to include information about the manufacturer, the product’s performance characteristics, and the permitted product licensing agency, testing center, evaluation organization, or Miami-Dade Notice of Approval (NOA). Please be aware that these criteria may change based on your specific region within the state of Florida.
Design Wind Pressures And Water Infiltration
Several parts of the code specify the testing criteria for windows. Section 1709 of the Florida Building Code, Building (FBCB) and Section R609 of the Florida Building Code, Residential (FBCR) mandate that windows be inspected and identified as adhering to AAMA/WDMA/CSA101/I.S.2/A440 or TAS 202. TAS 202 mandates compliance in the High-Velocity Hurricane Zones. The goals of these inspections are to determine how much air and atmospheric pressure, as well as how much precipitation, can get inside a structure.
The labeled DP number must match or surpass the minimum design wind pressure as calculated by the FBC or ASCE 7. The Performance Grade (PG) Number is the most significant indication on the accreditation sticker in terms of wind forces and water penetration. The PG Grade is directly linked to water penetration efficiency as well as the design pressure rating. For instance, if a product was tested at 15 or 20% water infiltration at 50 psf (depending on the product class), the PG Grade would be 50. This is especially essential in Florida due to the wind-driven rain caused by storms.
Check that the PG rating of the windows matches or surpasses the minimum design pressure rating. In the High-Velocity Hurricane Zones (HVHZ), the sticker must also include a Florida Product Approval number and a Miami-Dade NOA number.
Impact Protection
In some parts of the state, the FBC mandates that windows be impact resistant or secured by an impact-resistant covering like a storm screen, even though most people are aware of the need to secure glass during hurricanes. “Wind-borne Debris Regions” (WBDR) is what the FBC classifies these places. In regions where the design wind speed is 130 mph or higher, as well as in areas where the design wind speed is 140 mph or higher, the WBDR applies.
Laminated glass, which is offered in the form of impact-resistant glazing, is also included in the category of safety glazing. Clear glass sheets are joined with a plastic-like layer (typically polyvinyl butyral) in between them to create laminated glass. This “filler” inside the glass, which usually ranges in thickness from .015 to .090 inches, serves to keep the pieces of glass from breaking apart on contact. Broken glass remains contained within the polyvinyl butyral layer, stopping high winds from penetrating the structure and causing severe damage.
Keep in mind that reinforced glass windows have more robust frames than regular windows. The frame needs to be sturdy enough to remain in the aperture after being hit, despite the fact that the laminate will keep the glass intact. The entire window, including the panes of glass, the frame, the fasteners, and the installation method, are subjected to rigorous testing. Products made to shield windows and doors must pass stringent wind load and wind-borne debris tests before they can be sold.
Tempered Glass Windows
Although tempered glass is used in safety windows, it is not impact proof on its own. Glass can be “heat-treated” by heating it and then quickly cooling its surface, resulting in tempered glass. As a consequence of this procedure, the glass’s interior will stay warmer than its exterior. As the center thickness cools, it compresses the surfaces and edges. When tempered glass breaks, it shatters into tiny shards that aren’t dangerous to anyone nearby. This occurrence, also known as “dicing,” significantly decreases the chance of harm from human contact.
The FBC details which places should not have windows installed due to potential danger. Safety protection, such as tempered glass, is obligatory in these high-risk areas. Dangerous sites include those with a high probability of human contact, such as those in or near door components, near baths, on handrails, and glass adjacent to stairways. Section 2406 of the FBCB and Section R308 of the FBCR outline the specifics of what constitutes a dangerous environment.
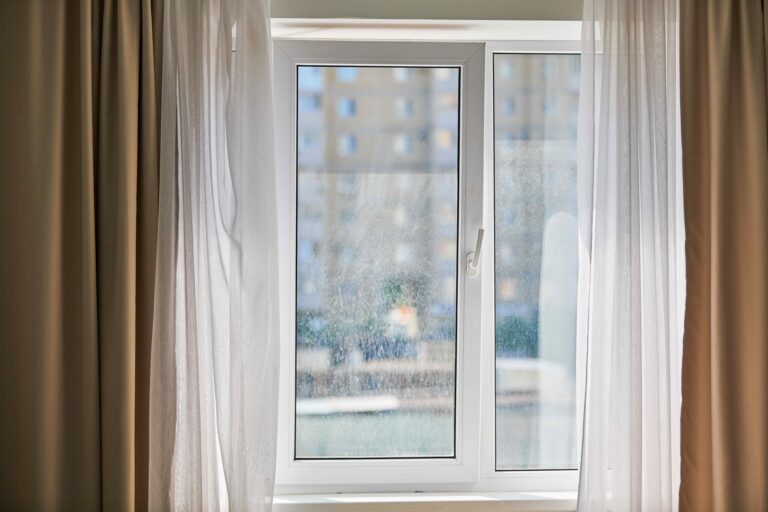
Replacement Windows
Replacement windows are a viable option for many property owners and managers because of the constant evolution of window technology. There have been significant improvements in the efficiency, upkeep, and usability of windows over the past few decades. According to Section 105 of the FBCB, obtaining a permission is necessary before replacing windows in Florida, and in some cases, compliance with other building codes may also be mandated.
No matter how recently a building code was enacted, pre-existing structures are generally allowed to continue to serve their intended purpose without modification. However, the Florida Building Code, Existing Building (FBCEB) Provisions would apply to the removal of windows for any purpose. All work done on an established structure, including maintenance, renovation, repurposing, expansion, and relocation, must comply with the FBCEB.
At this point, you should understand how important it is to work with an accredited installer when adding or replacing windows in your building. An installer’s certification ensures that the standards for window safety, design, wind pressure ratings, water infiltration, impact protection and tempered glass are met. Furthermore, their expertise allows you to feel confident that any window installation is up to code and in compliance with the current building regulations of Florida. Your satisfaction is our number one priority – so don’t leave the process of window installation to just anyone. Let us help you rest assured knowing your new or replacement windows are expertly installed at a reasonable price. Don’t hesitate – contact us today and let our team give you peace of mind when it comes to your window installation needs.
Let Us Help You Understand Florida Building Codes For Ideal Window Installation